The new S170 has CNC machined aluminum lugs bonded to alloy tubes
Atherton Bikes still seems relatively new, but the brand is already five years old. And, up until now, it’s been making frames using an additive manufacturing processes, hence the AM tags. During that time, it has refined the production process a fair bit and grown a great reputation for its distinctive carbon-tubed AMs that now span from a 130mm trail bike up to a 200mm travel, multiple World Cup-winning, DH bike. Charlie Hatton also won a World Championship gold medal on one.
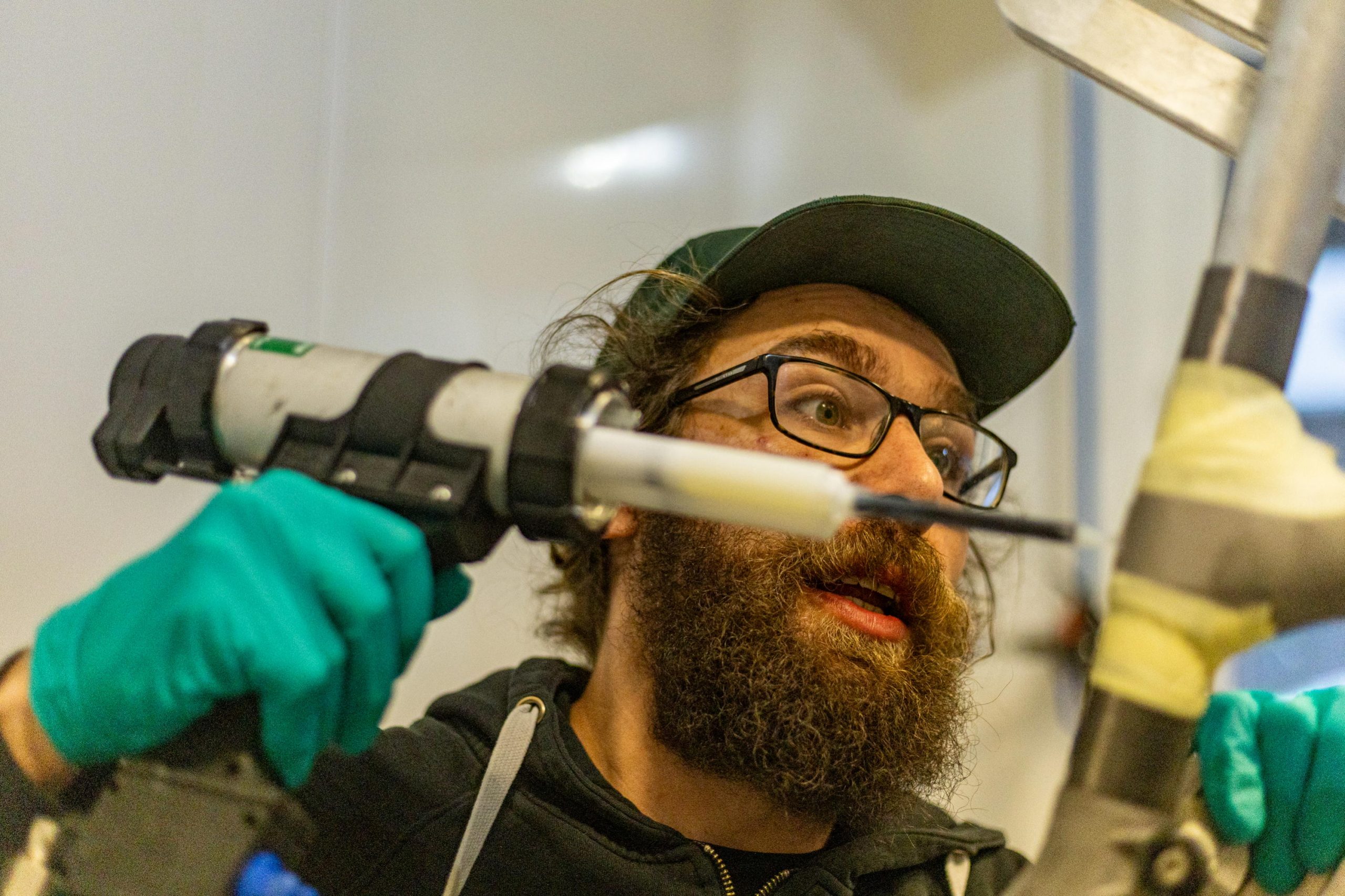
Forget welding, the Atherton S170 is bonded together just like the AM170
All Atherton models to date have been made in Wales and tested (largely by the family themselves) just up the road at Dyfi, where they rather conveniently own and run one of the world’s best bike parks. Keeping everything local and in-house doesn’t mean the finished product comes easy though when production involves bonding custom round carbon tubes into 3D printed titanium lugs that are laid down on a mega-money laser machine over sixteen hours.
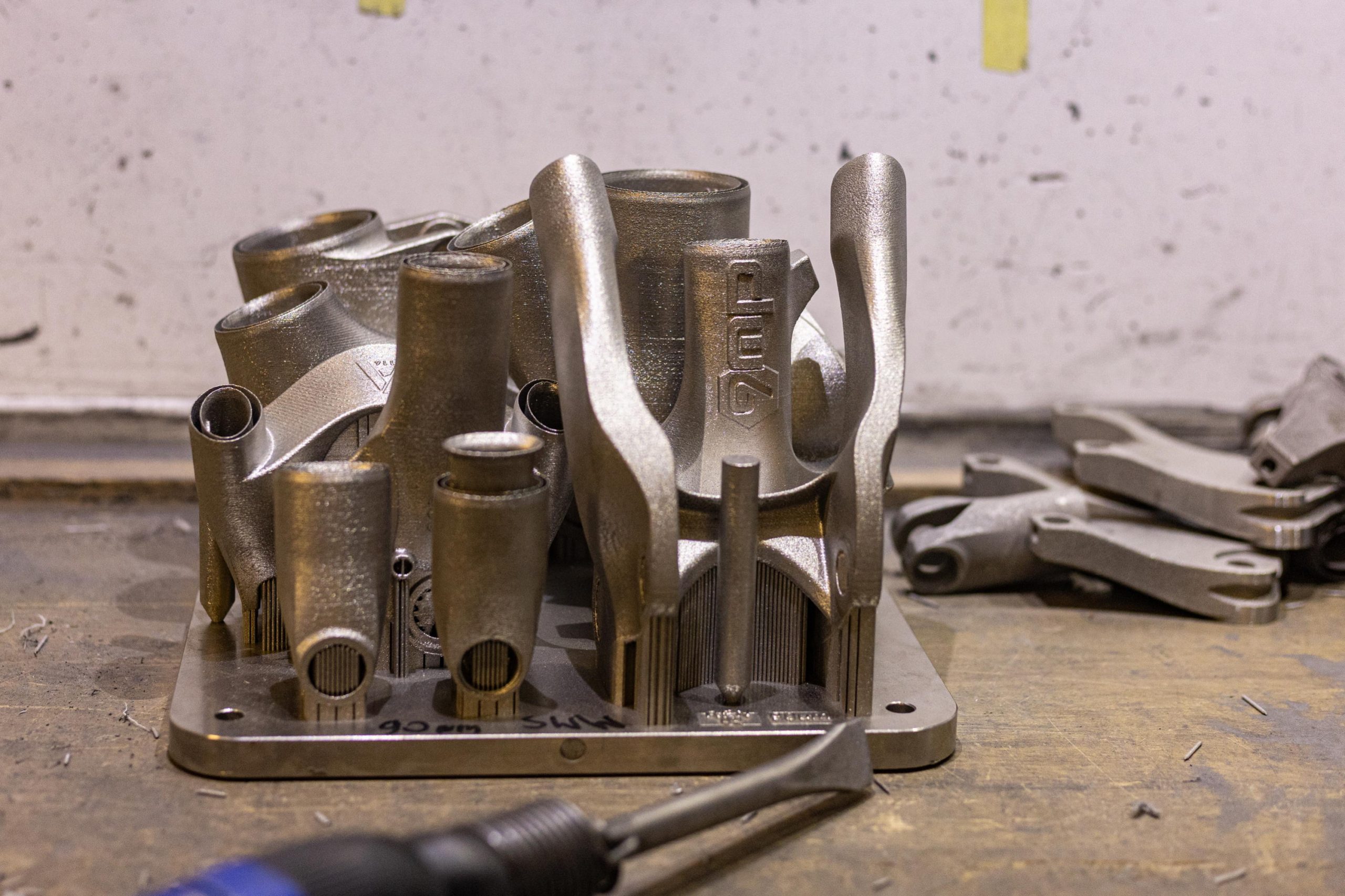
The AM170 has 3D printed titanium lugs
And, if the laying layers of titanium powder part wasn’t time consuming enough, the lugs and hardware still require heat treating and a lot of hand finishing with the bike engineers’ equivalent of dentist drills before they can actually start to bond a frame together. In short, this means Atherton Bikes can currently only produce 300 frames a year without investing in more ludicrously expensive Renishaw lasers. Who knew making custom bikes by hand in your own facility with zero compromises might prove very time-consuming and expensive?
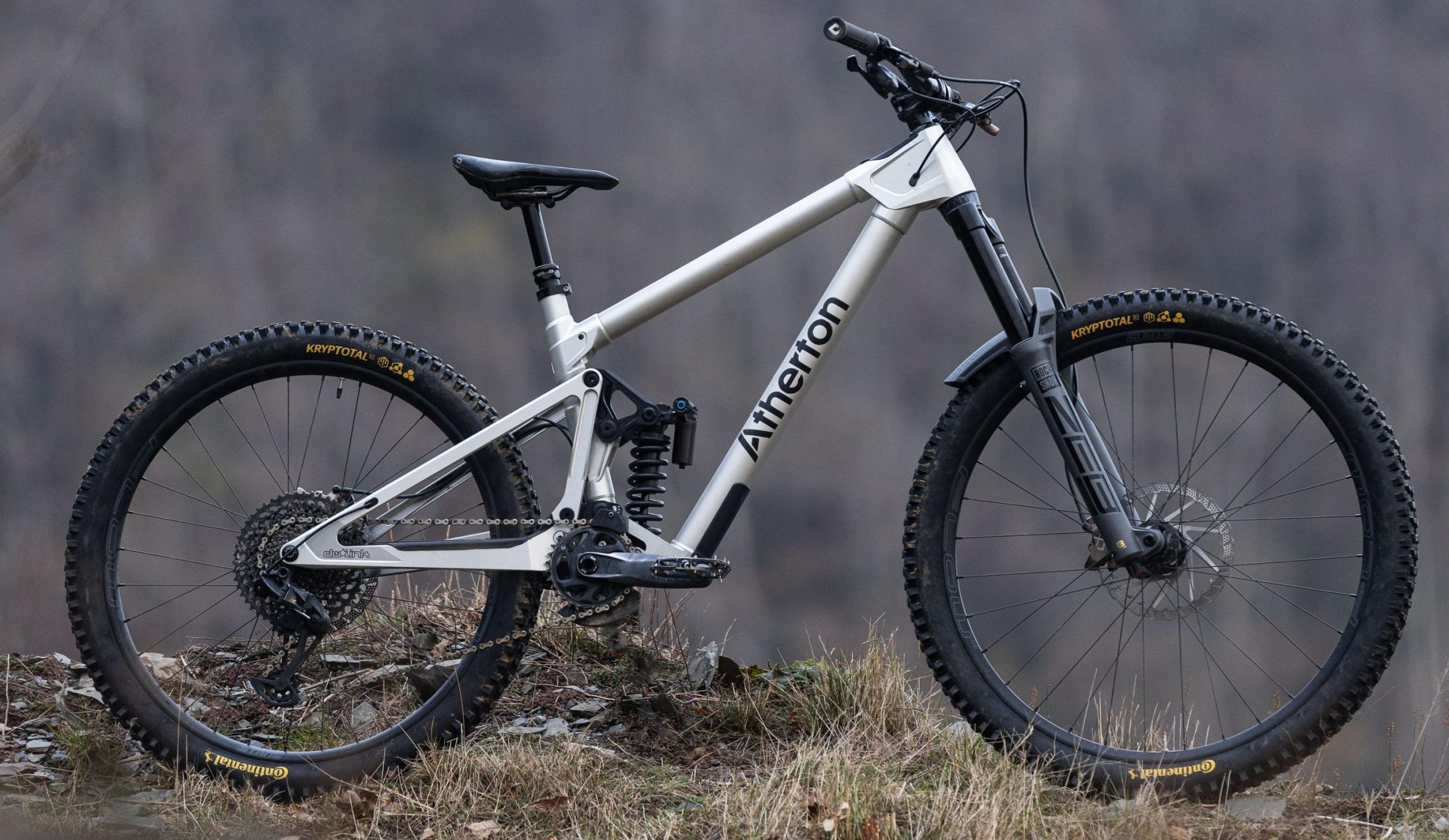
The new Atherton S170 uses bonded alloy lugs and tubes to reduce costs
Atherton Bikes S170 need to know
- Frames optimised for strength
- 7075 alloy tubes bonded to CNC machined alloy lugs
- New lower price points
- S stands for subtractive CNC machining process
- 12 frame sizes to choose from
- DW4 suspension with 170mm travel
- Geometry designed around a 180mm fork
- MX wheels with Conti tyres
- Bikes assembled in Wales
- Three builds, and a frame option for £2,799
Enter the all-new S170. This is the brand’s big mountain 170mm rear travel enduro bike built fully from aluminium. And it’s taken direct inspiration from the superb AM170 with mixed 29/27.5in wheels I tested last year. Using aluminium instead of carbon tubes represents an all-new way to make Atherton Bikes that are cheaper yet still kind of look the same.
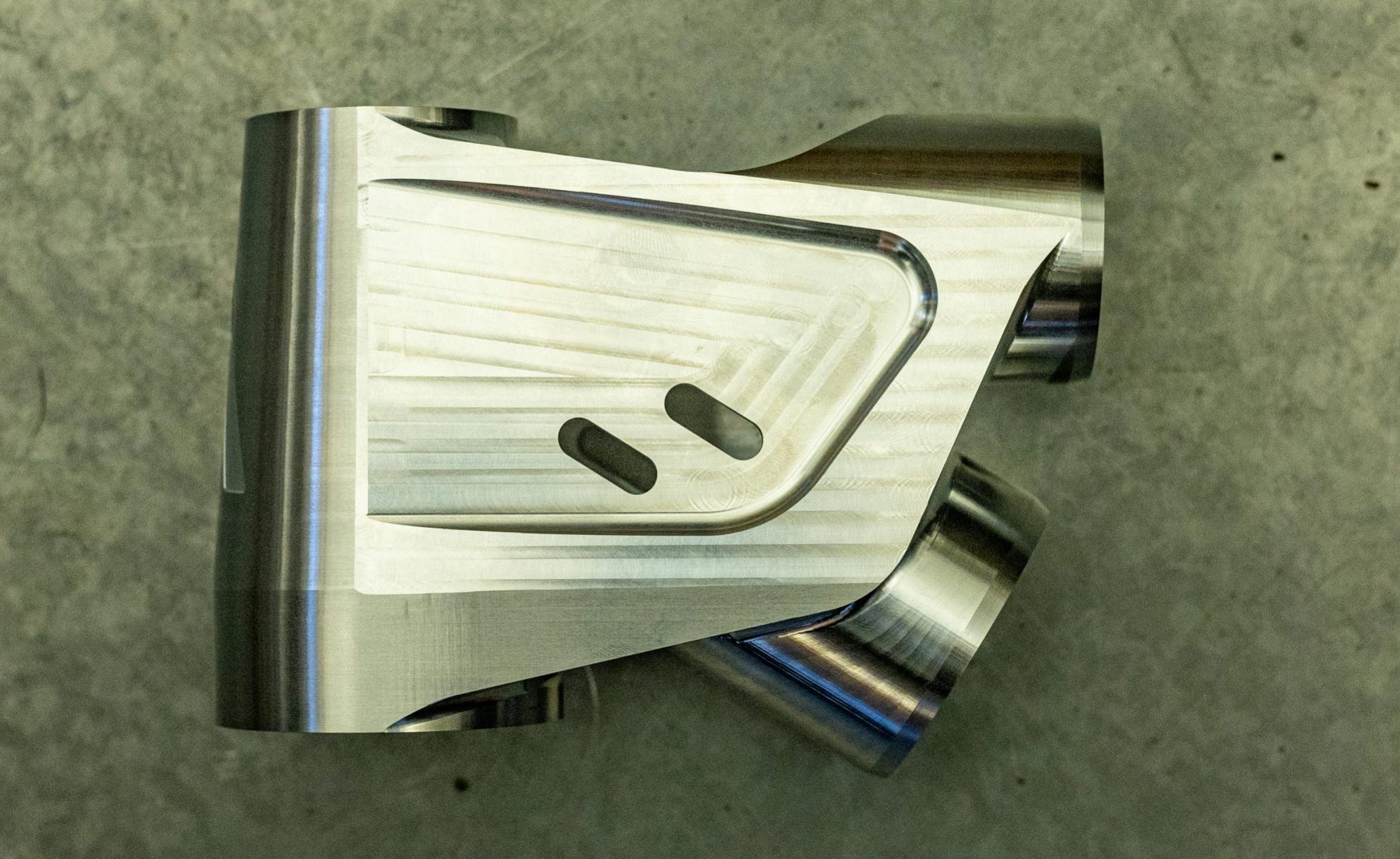
The machined lugs on the Atherton S170 give it a distinct look
CNC machined lugs and alloy tubes
The ‘S’ model achieves this by using a subtractive manufacturing process, which sees the CNC’d lugs machined-away rather than built up like the additive titanium pieces that form the joints of the AM skeletons. Machining the lugs with a computer-controlled cutter means Atherton Bikes can glue in round extruded aluminium tubes and maintain 12 unique size options and its distinctive frame silhouette.
And the S170 definitely shares a family resemblance, but the brand explained the new production process is about much more than just looks. Bonding, instead of welding, allows Atherton Bikes to use stronger 7075 aluminium that offers 70% higher fatigue performance and 70% higher ultimate tensile strength (UTS) than weldable alternatives such as 6061. Another benefit of bonding, is that it avoids heat-affected zones and potential distortions that can affect tolerances and even geometry on welded aluminium frames.
Patent pending lug design
The brand’s experience with bonding sees the S170 use similar hollow double-lipped lap shear joints to the carbon bikes, but the exact build process is currently secret and the subject of a patent application – presumably due to the ease with which rivals could ape the CNC mass-produced part of the process more easily than the cost/time restricted 3D printing method used on the AM bikes.
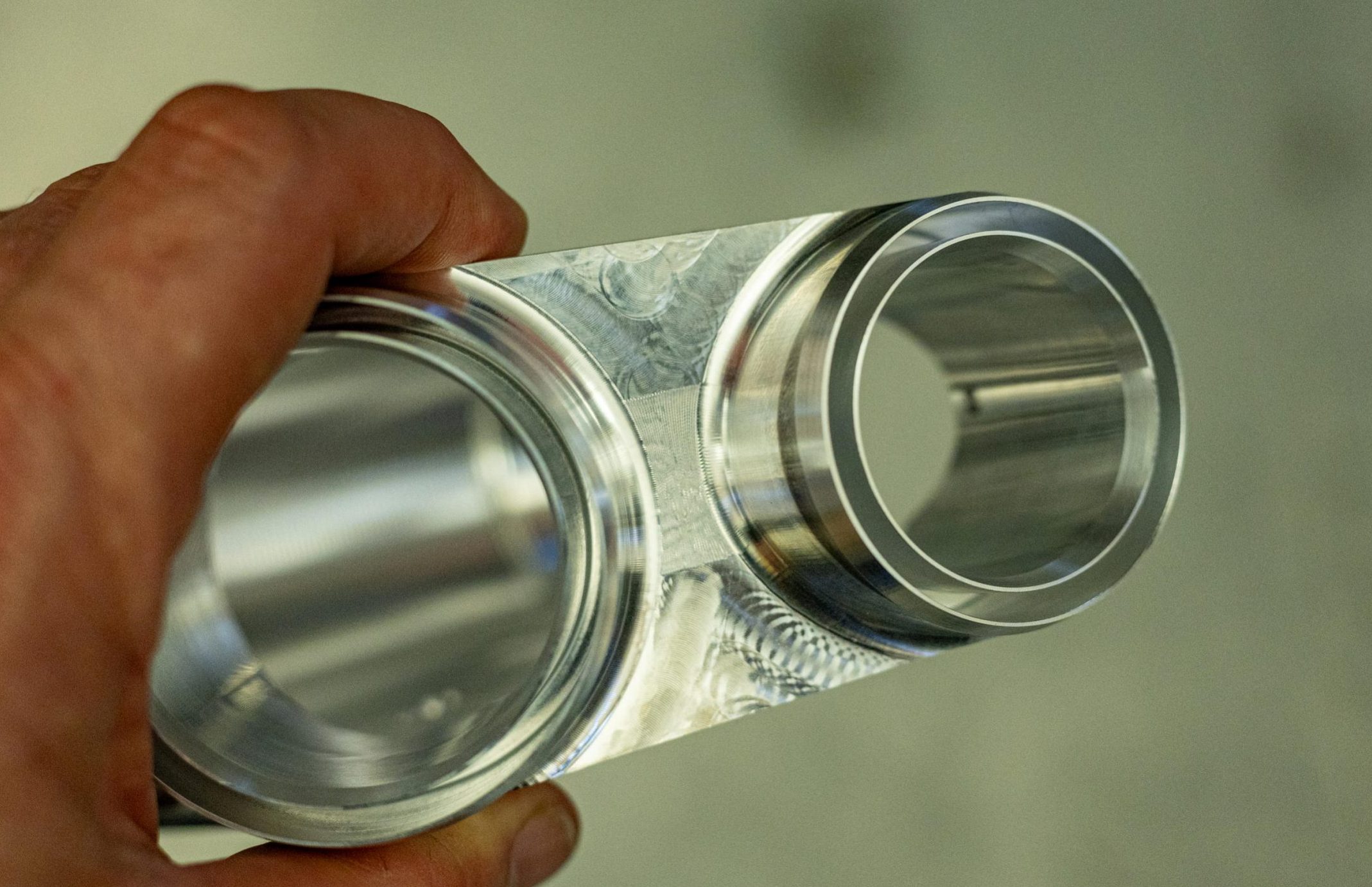
Alloy tubes are bonded directly to the lugs
When pushed about the manufacturing process, all I could get out of Atherton Bikes was that the frame is clear anodised to resist corrosion and the 7075 tubes themselves are plain gauge. Also the CNC-machined lugs are shaped in a way that act like butted tubes and vary in thickness from end-to-end – in much the same way a hydroformed tube has thicker material at the ends of frame members and is thinner in the middle. Built like this, the S170 tube joints are moved away from peak loads too, ‘We use a CNC machining process to create a localised monocoque structure. This optimises the weight of the aluminium, plus transfers the load from the tubes to the lugs in the most stress-efficient manner possible.”
It’s not all made in Wales
So, the new aluminium frame is still assembled in Machynlleth, but the fresh material crucially offers the ability to massively scale production. With a new facility across town it will have capacity for 5,000 S frames/bikes once running at full speed. So look out for more job opportunities the brand is bringing to the area. Initially there will be limited availability of the S170 until the team moves fully to the new site in coming months.
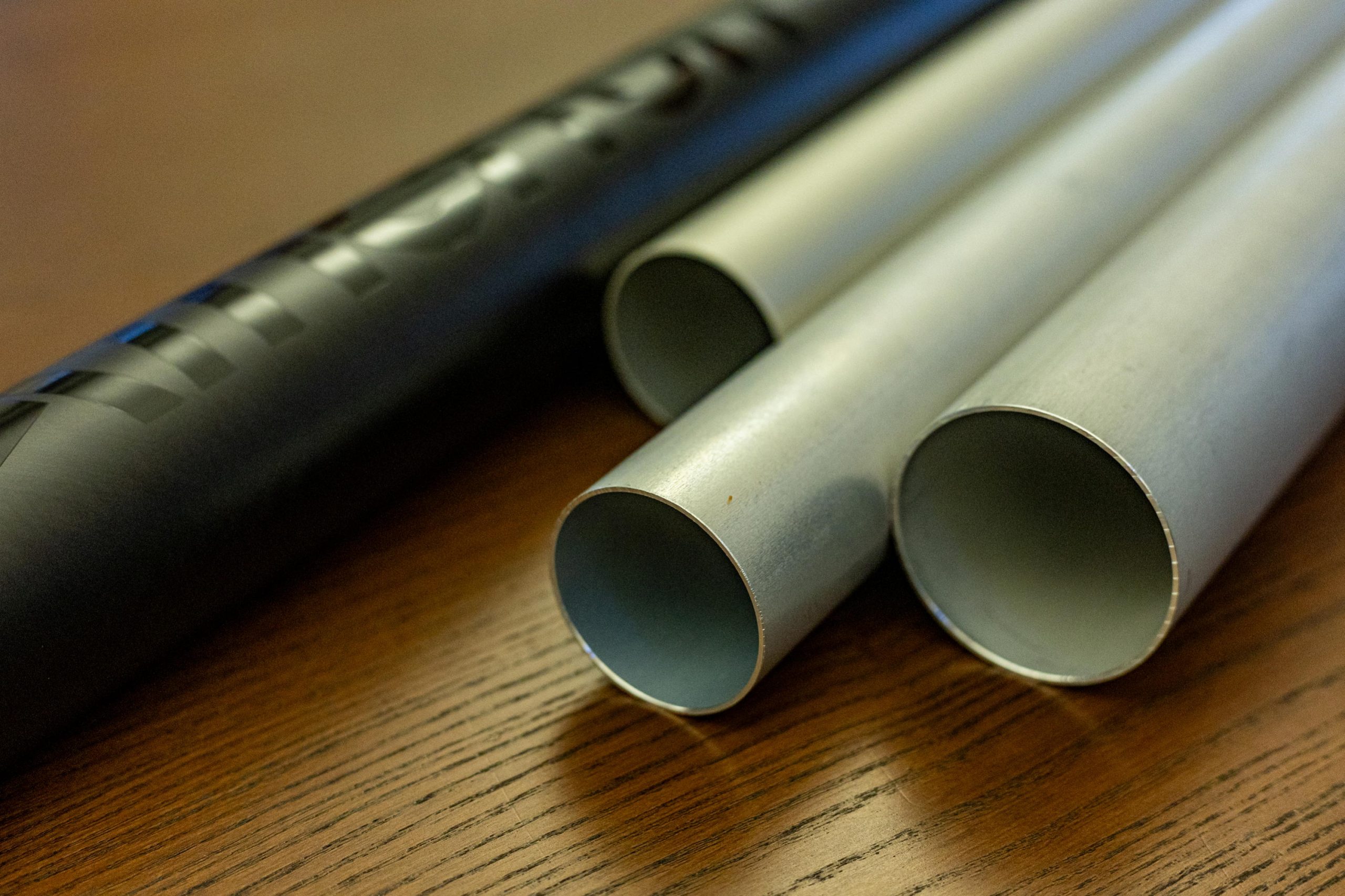
For the S170 Atherton bikes swap carbon tubes for alloy
Key aluminium pieces are machined overseas, and the brand also showed us a big stash of 7075 tubing and how the bonding process is simplified and much quicker on the S170. The S frames will come with the same degree of quality control, built-in-Wales stamped on them and should be as tough as their carbon sibling with even better impact and damage resistance on the tubes. Durability is a big deal for Atherton Bikes and I was told it’s a key priority here to offer a bike that can roll with the punches and last for years without smashing to pieces like too many frames they’ve seen demolished at Dyfi bike park since they opened.
Same geometry as the AM170
And, since the S170 mirrors geometry and suspension knowledge garnered from the AM170 and most of the plentiful sizing options where reach grows in tandem with seat tube angle, seat tube and chainstay lengths, ride and fit should be totally sorted. And it doesn’t take a genius to see how the brand could roll out this production process to its DH and trail bikes too, so watch this space.
So far, I’ve talked a lot about the similarities between the new S170 and the original AM170, but there are also pretty significant differences; not least an entirely different suspension platform. The S170 gets Dave Weagle’s older 4-bar DW-Link design, rather than the more tuneable DW6 layout. There’s also the obvious addition in weight with the material swap that sees the 465mm reach (size 7) S170 weigh a chunky 17.4kg on my scales, which is a kilo more than the carbon version I tested. Lightweight carbon is obviously part of this, but the precision with which Atherton Bikes can lay down the exact amount of titanium needed in the 3D printing process is also a factor compared to the less accurate and heavier alloy lugs on the S170.
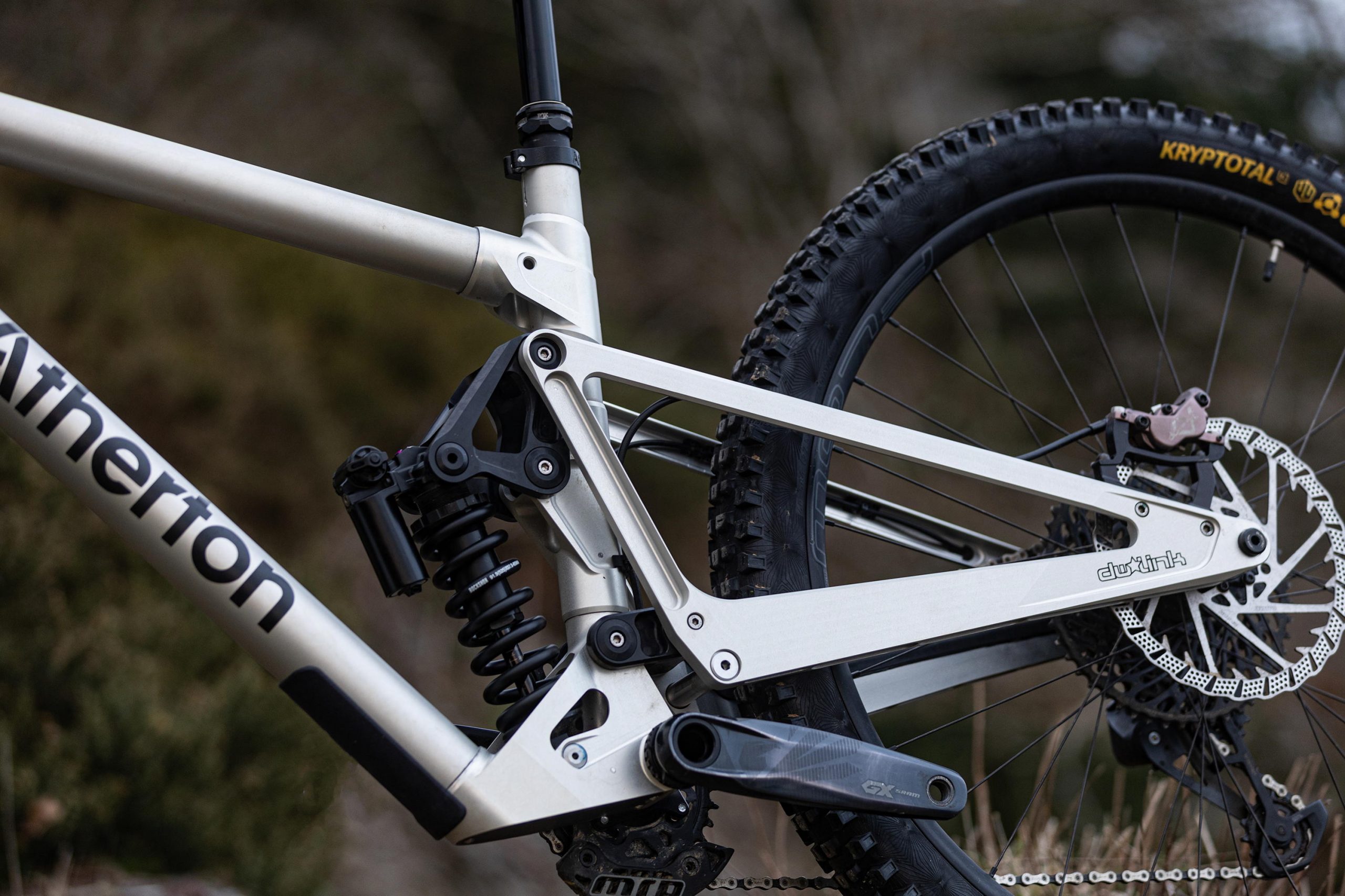
Twin-link DW4 suspension rather than DW6
DW6 swapped for DW4 suspension
You don’t need to look too intently at the S170 back end to see one of the key differences between what Atherton BIkes is calling DW4 and DW6 suspension is a triangulated aluminium rear end, rather than the multiple limbs and chainstay pivots on the AM170. This last part is an important aspect of maximum tuneability on the AM bikes, but adds complexity, extra bearings and cost. Engineer Rob Gow explained, ‘DW4 can offer the same top-notch performance, but is cheaper, simpler and easier to maintain. The S bike was a complete evolution built off the AM170, so a lot of the suspension fine tuning had already been done and it was easier to replicate the numbers on the DW4 design to get close to the desired performance straight away.’
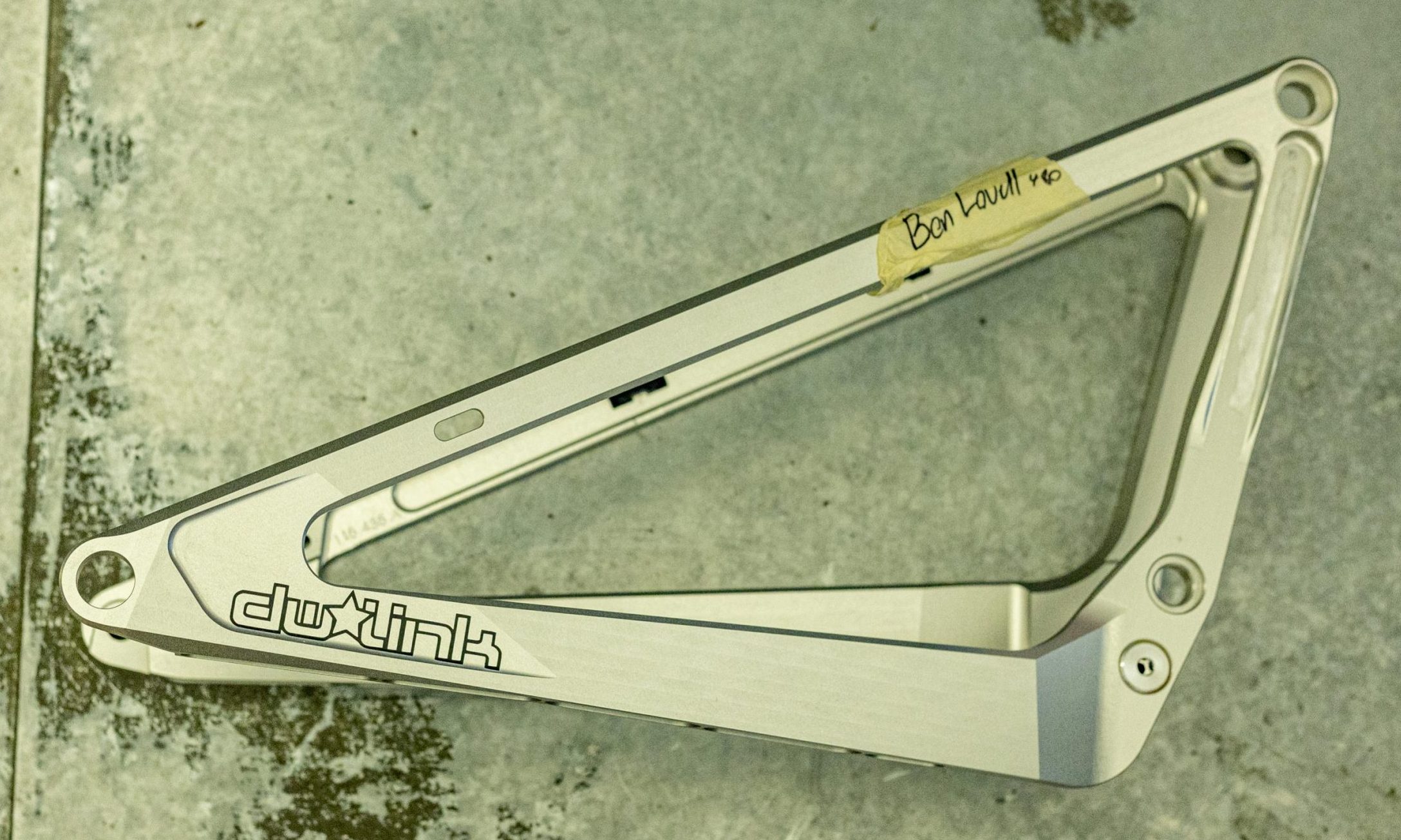
Sleek machining on the alloy swingarm
Flex engineered into the rear triangle
This asymmetric aluminium rear end is manufactured overseas, just like the CNC’d parts and has been through numerous revisions to try and match the AM ride feel and flex characteristics. The latest production version is quite flexible to touch and you can even twist the flat L-shaped seatstays a little by hand, with the L-shaping presumably promoting the desired ride feel and also allowing rear cables to route hidden from sight. Underneath, there’s a thinnish rubberised chainstay protector, and the whole thing joins a complex machined BB section that extends down and forwards to cradle the lower end of the shock. The look of this part definitely has a bit of an old-school Iron Horse Sunday or even Giant Reign vibe to it; unsurprising as both of those bikes used similar short twin-link suspension designs.
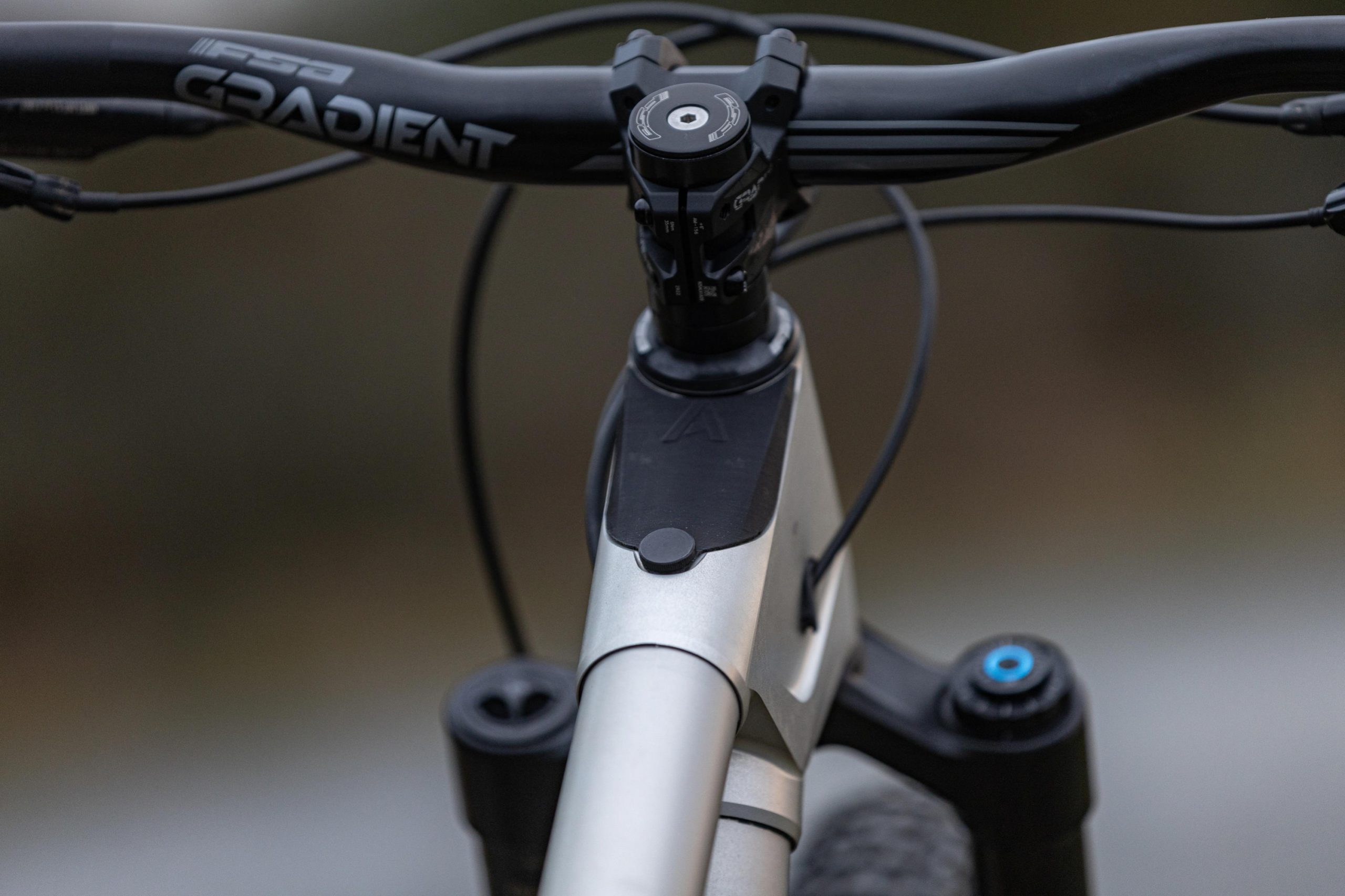
Potential stash box built into the head tube lug
Inside the 7075 aluminium tubes, S170 cables are routed in quietening insulation and there’s a removable cover over the main headtube junction which the brand says can also be a miniature frame stash at some point in the future (although it has more to do with the production process allowing access to cut away maximum material than accessing anything inside).
Not as plush as the AM170
The original AM170 was Dan Atherton’s pet project to create a machine he can do-it-all on, and he’s also done a lot of the testing on the S170 prototypes that have been floating around for a couple of years. Dan reckons with the geometry and sizing the same, the only real difference is in suspension performance, and in particular, small bump absorption. Where Dan sees the AM170 as class-leading in terms of tracking and comparable with most DH bikes (I’d largely agree), the S170 is slightly less smooth, which may be down to materials as much as the suspension design. He also reckons that once deeper into the travel, it’s hard to tell the pair apart.
Other Atherton athletes and team members have had their input too and the final ride-tuned S170 chassis is available as a frame only option or in three different build kits. Aluminium saves cash, but being more affordable than the totally custom-built AM models doesn’t exactly mean cheap; the aluminium frame alone is £2,799 (with a Fox DHX2 shock) and complete builds start at £4,799 for the cheaper RockShox Domain build, up to £5,999 for the RockShox Super Deluxe/Zeb/GX Eagle version I tested at Dyfi. There’s also a Fox Performance model in between for £5,499, and all models use a 180mm fork and Conti’s latest tyres and Hayes Dominion A4 brakes that the race team use.
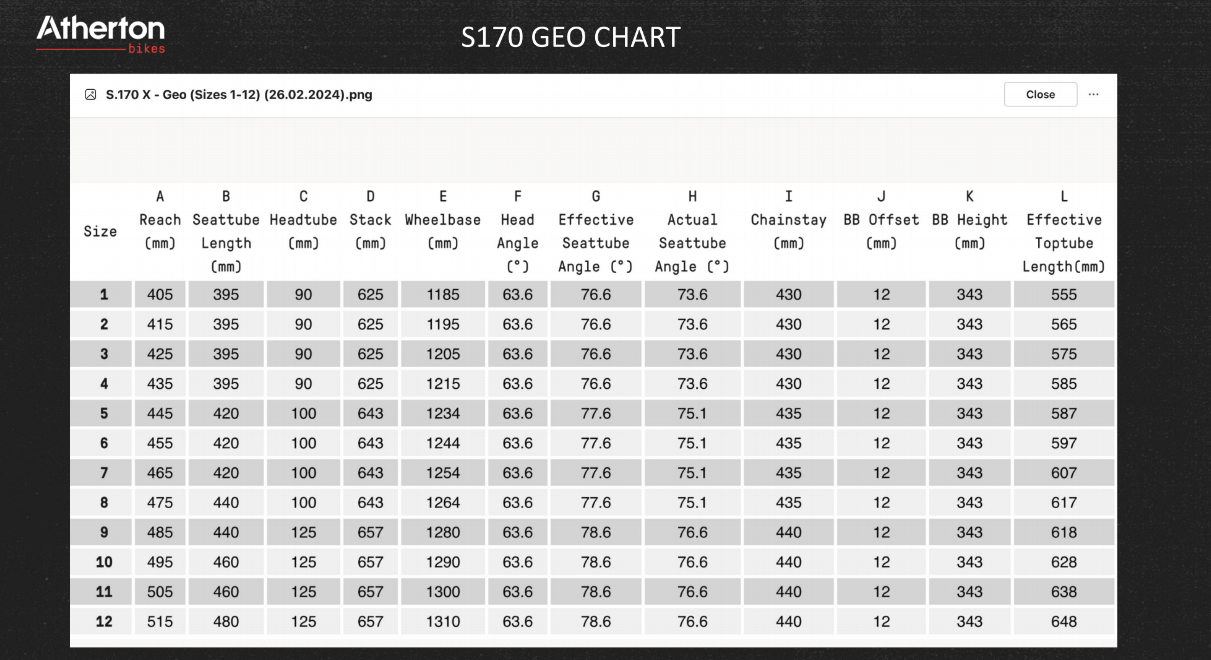
How many bike brands offer 12 unique sizes?
12 frame sizes for the perfect fit
Twelve sizes are obviously a lot, but that’s still less flexibility than the line-by-line customisation offered on the AM range. Also fixed S170 build options mean you can’t mix and match parts or chainstay length to taste either, like on the flagship AMs. Atherton Bikes aims to have some key sizes available off the shelf in six months, and in case you’re wondering about dual crown compatibility on a bike like this, the brand hasn’t tested for it yet, but seems likely to rate it once it gets the testing done.
How the S170 rides
So that’s all a lot of information about the idea and tech behind this new concept, but how does it actually ride compared to the AM170? And, perhaps more importantly, the kind of long-travel enduro bikes from other brands it’s going to be up against with a £6K price tag. I only managed about 5 runs at Dyfi in my limited time on an early S170 with a couple of rogue parts and wasted a chunk of the day fiddling with spring rates and suspension settings, so a full review will have to wait until I get the bike back. I’m not paid to say ‘no comment’ though, so I will stick my neck out with a few initial thoughts.
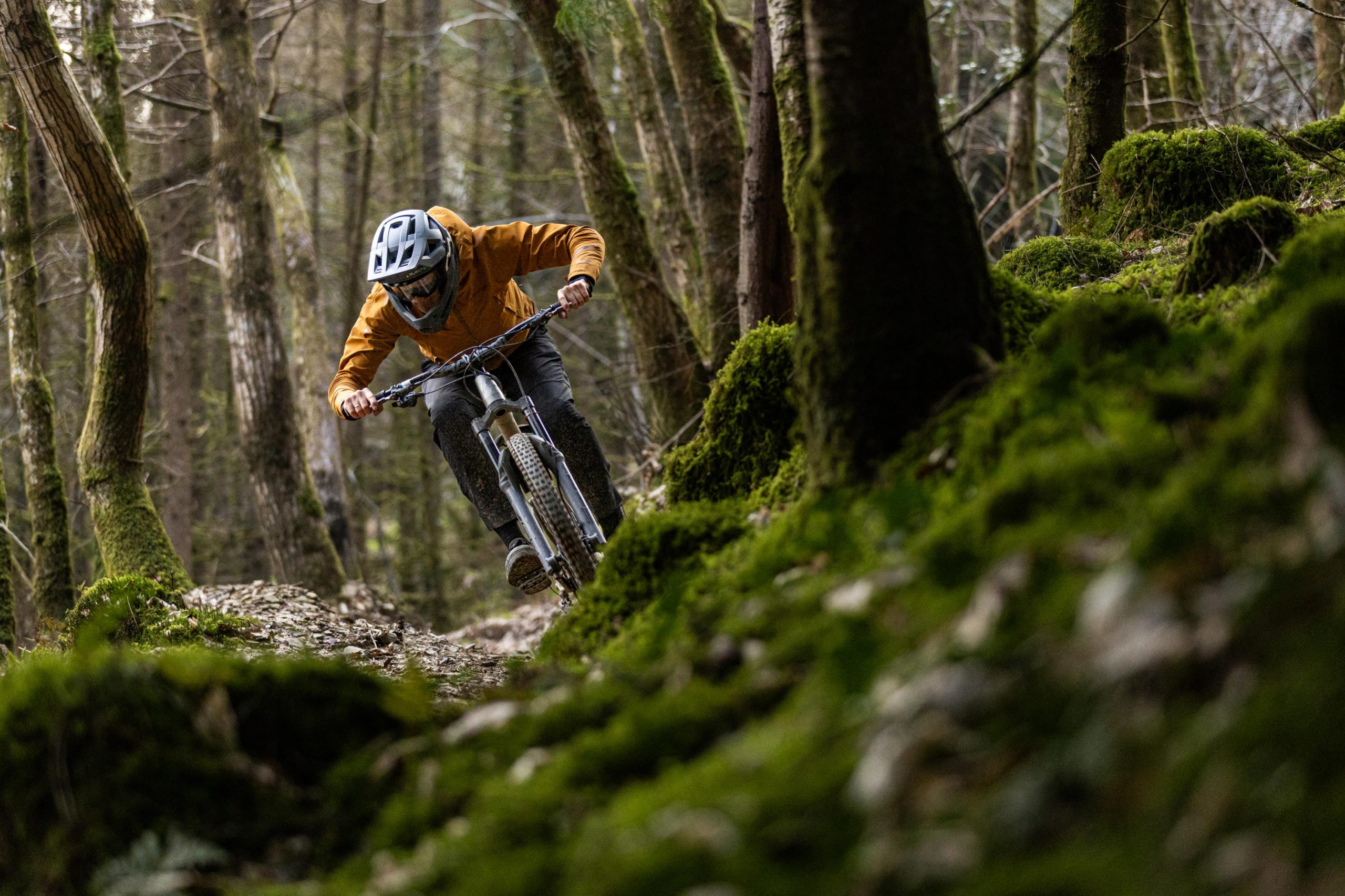
First impression were that the S170 wasn’t as plush as the AM170
Aside from the geometry and steering, I’d echo Dan Atherton about the similarities and also that the bike doesn’t have the ultimate smoothness of the AM. It also feels noticeably different to me to the AM170 in terms of suspension support and rider balance/position (which maybe isn’t that surprising considering it uses a different suspension platform and is made out of a different material and had a different specification. Where the carbon bike has a smoothness that dulls most small bumps and vibration to make the bike super calm, here, it’s much sharper. The S170 still has the same ‘trucking on’ speedy ride and balanced geometry to keep the rider calm, but you can really feel what’s going on underneath at the wheels through the machine itself. If you’ll indulge my first impression, it’s of a bike with something of a race car feel and being strapped into a harness of an open-roofed Caterham or something bombing around with the wind in my hair and bum inches off the floor, rather than deep leather seats and German-engineered ruthless efficiency of the AM170.
Overall it’s a solid bike
One thing’s clear though, the S170 has the basic bones of a sorted bike with a unique look and production method that potentially offers genuine advantages. It isn’t light by any stretch, but holds good pace across the ground and never feels like a heavy old dog pedalling, riding dynamically or when climbing. It should also be super strong with those solid 7000-series tubes.
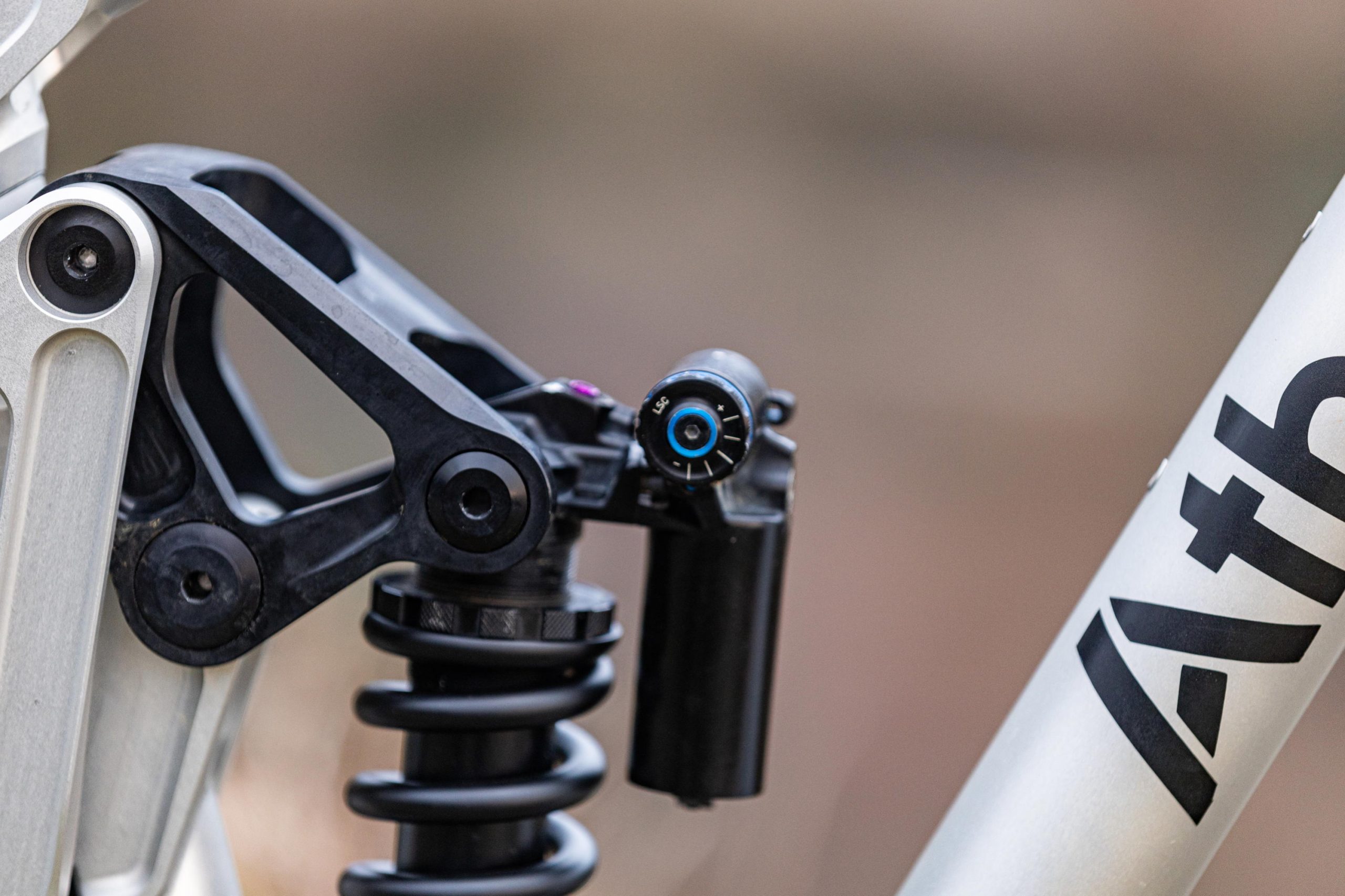
With a different shock tune the Atherton S170 could be better
Atherton has probably done more S170 tuning and development with Fox DHX2 shock (the race team are on Fox and I’ve seen Fox kit on Affy’s bike during development) and my sense is this RockShox Super Deluxe-equipped model is potentially overdamped, but that’s an easy enough fix, and, ironing out a few creases was exactly the same deal when Atherton Bikes first launched its AM150 five years ago. The brand made the right subtle tweaks there and totally dialled those bikes in and can hopefully do the same here.
I’m going to head back to Dyfi for another go on a S170 and will report back soon with a separate full ride review on whether this unique aluminium machine has the potential to grow Atherton Bikes into a completely different sized proposition. Either way, the S170 is a unique engineering solution and represents a new phase for the Atherton masterplan that’s already having a massive positive influence on this corner of Wales in one way or another.