Focus looks to improve sustainability of high-end frame manufacturing with new thermoplastic tech. Could this be the eco-friendly future for premium mountain bikes?
Focus has revealed the tech it hopes will bring together the light weight and high-performance of a carbon frame with reduced emissions, sustainable manufacturing and an elongated product lifespan. The Jam2 NEXT is an e-bike frame built with recyclable thermoplastic carbon in a fully automated process. And it’s being made right here in Europe, cutting vulnerable supply chains and reducing transport emissions.
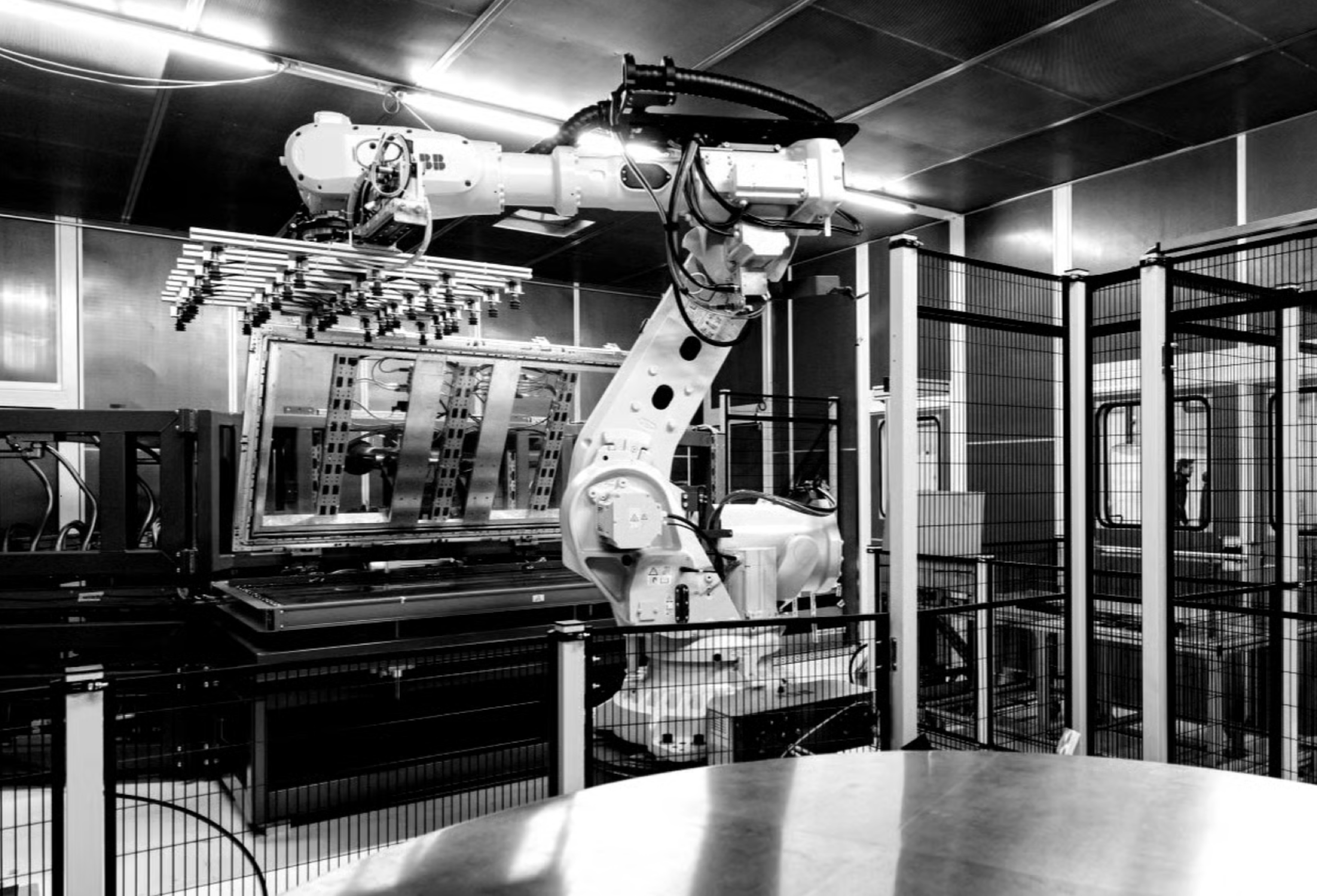
A huge robot will lay the thermoplastic carbon sheets into the mould. The process is much quicker than traditional carbon frame manufacturing.
The NEXT big thing?
This is not a new idea. Thermoplastic carbon manufacturing is used extensively in aerospace and automotive industries, among others. It is not even the first time it has been used in the bicycle industry; Guerilla Gravity used this process for its full-suspension bikes until it folded in 2023, while Forestal had plans to bring its e-bike manufacturing to Andorra with investment in this process when we visited the brand in 2022.
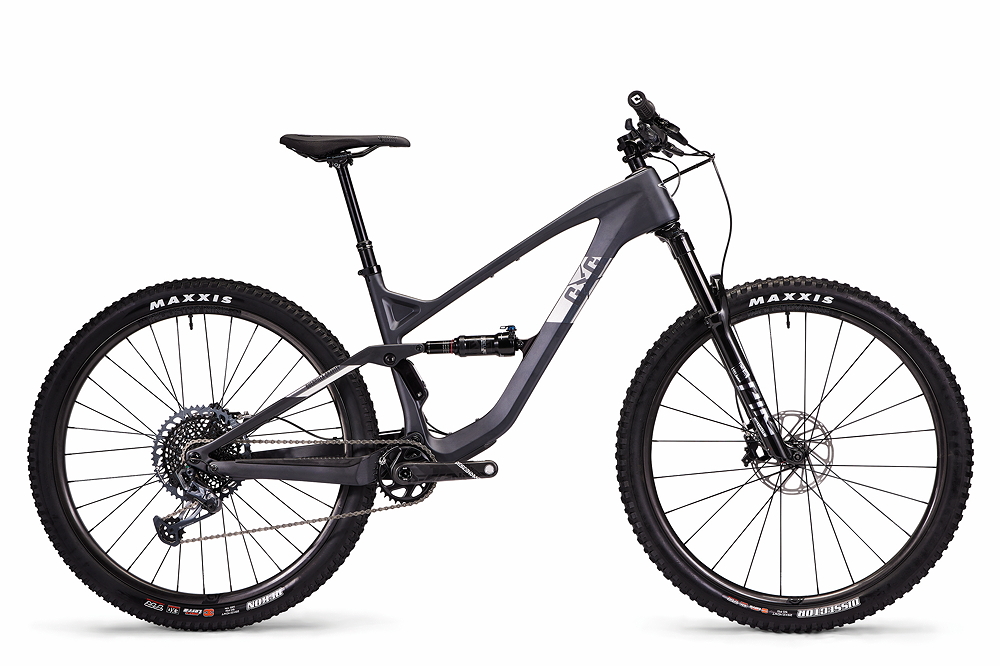
Guerilla Gravity used this tech to make its full-suspension frames in Colorado.
Canyon is also making noises in this arena, and at Eurobike 2025 the German direct-sales brand showed a machine that could make a one-piece carbon bar and stem in just one minute. Clearly there are other big players in the bike industry that are looking into this production method, particularly since Covid revealed the vulnerability of Asian supply chains, but so far none have publicly thrown their hat in the ring. Which makes Focus’s announcement significant, even if the Jam2 NEXT is not in production yet.
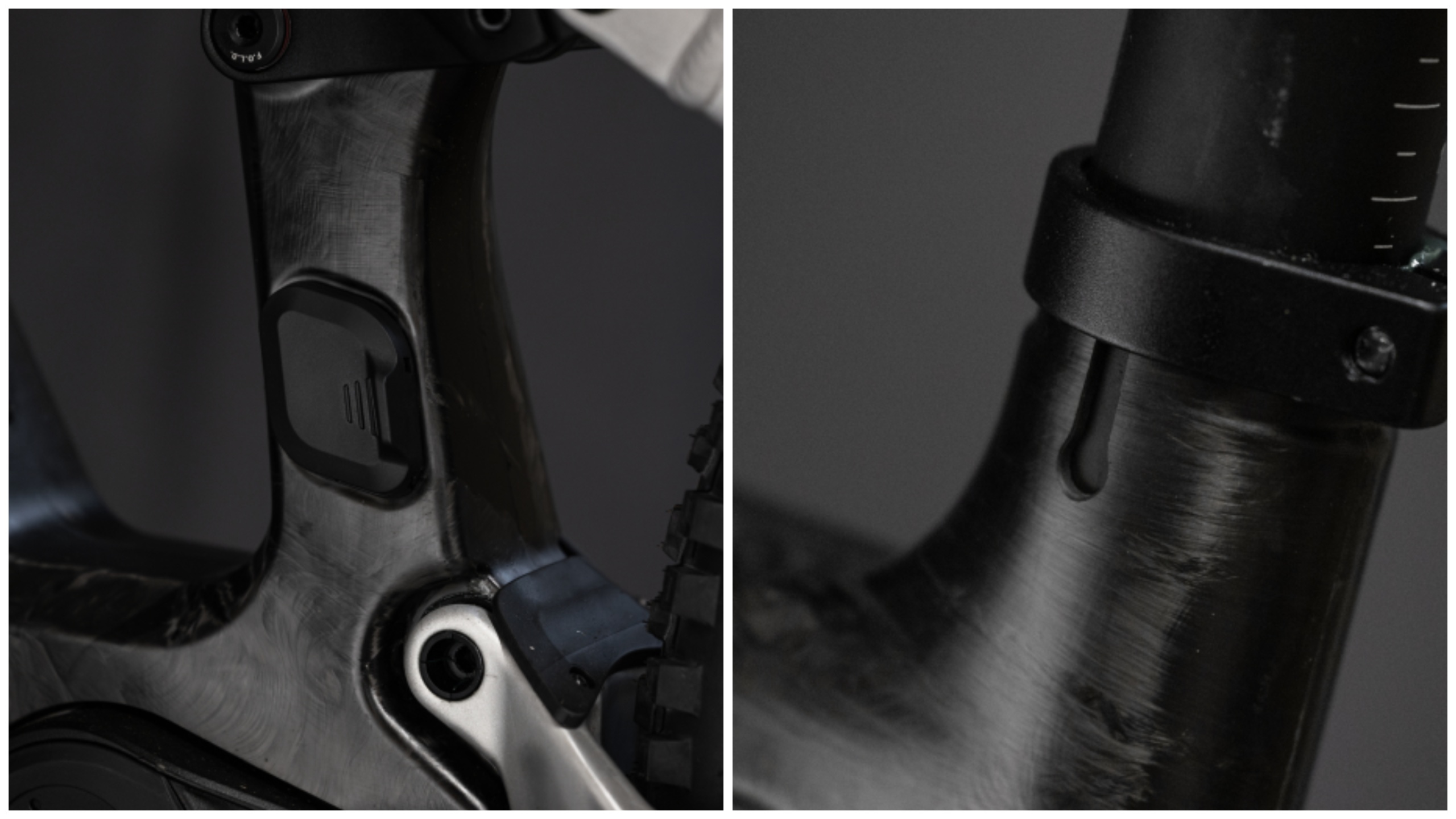
Focus had plenty of challenges in the development of the Jam2 NEXT frame to ensure it would be easily recyclable.
What makes this carbon recyclable?
So what makes this news so significant? Traditionally, carbon frames cannot be recycled into anything much at all. The process is to specialised and time-consuming to be worthwhile. Which means old or broken frames are largely scrapped, at huge cost in terms of emissions and resources. The thermoplastic approach allows the frame to be effectively chopped up, melted down and reformed into a new component. And this is because it uses a thermoplastic polymer to bind (glue) the strands of carbon together and lock the product into its shape. The difference being that here the glue can return to its original form, while the thermoset resin, as the name suggests, sets permanently.
“We definitely had to go through a number of additional loops and scrap plenty of first concepts to end where we are now”, explains Mario Pöss, lead engineer on the project.
“A good example is the incorporation of other materials. In traditional carbon manufacturing, metal inserts to mount shocks or other hardware are baked into the frame, or at least glued-in. You would then need to extract those before recycling, which isn’t possible in the first place with traditional carbon frames. So, we had to figure out ways to keep our frame pure – to make it convenient to recycle.
“The solution are threaded aluminium inserts that can be removed easily. At the end of its lifetime, it should be as easy as sorting waste at home. And potentially, inserts can even be re-used in a new frame after frame failure.”
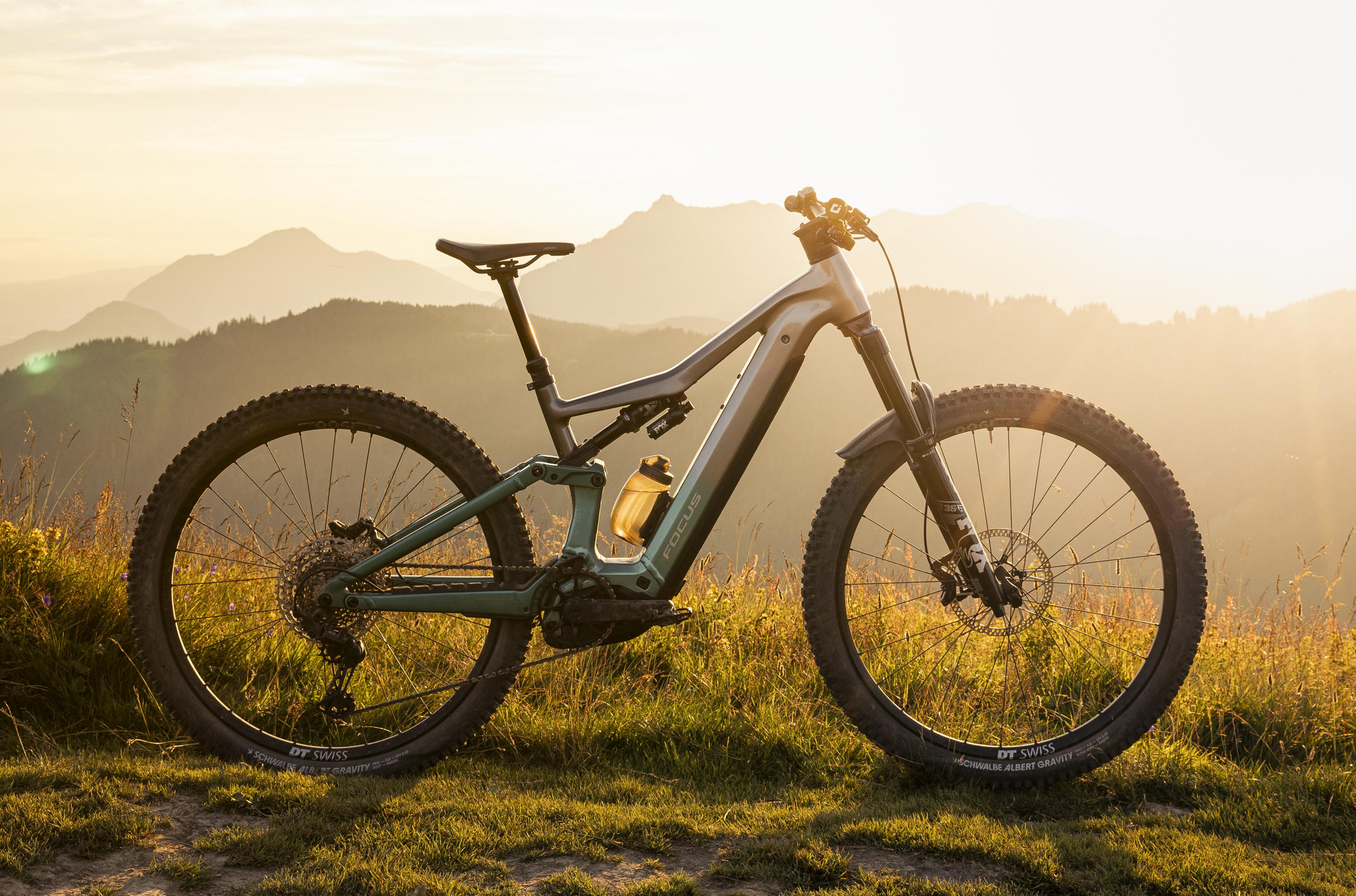
The current Focus Jam2 is only available with an alloy frame.
Faster and cheaper?
A further advantage to the process is that it can be automated. Robots can lay the thermoplastic sheets into the mould in significantly less time than it takes for a skilled human worker to individually place the thousands of pieces of carbon into a typical mould for a bike frame. So although the investment in machinery is significant, there is potential for cost savings per unit in production.
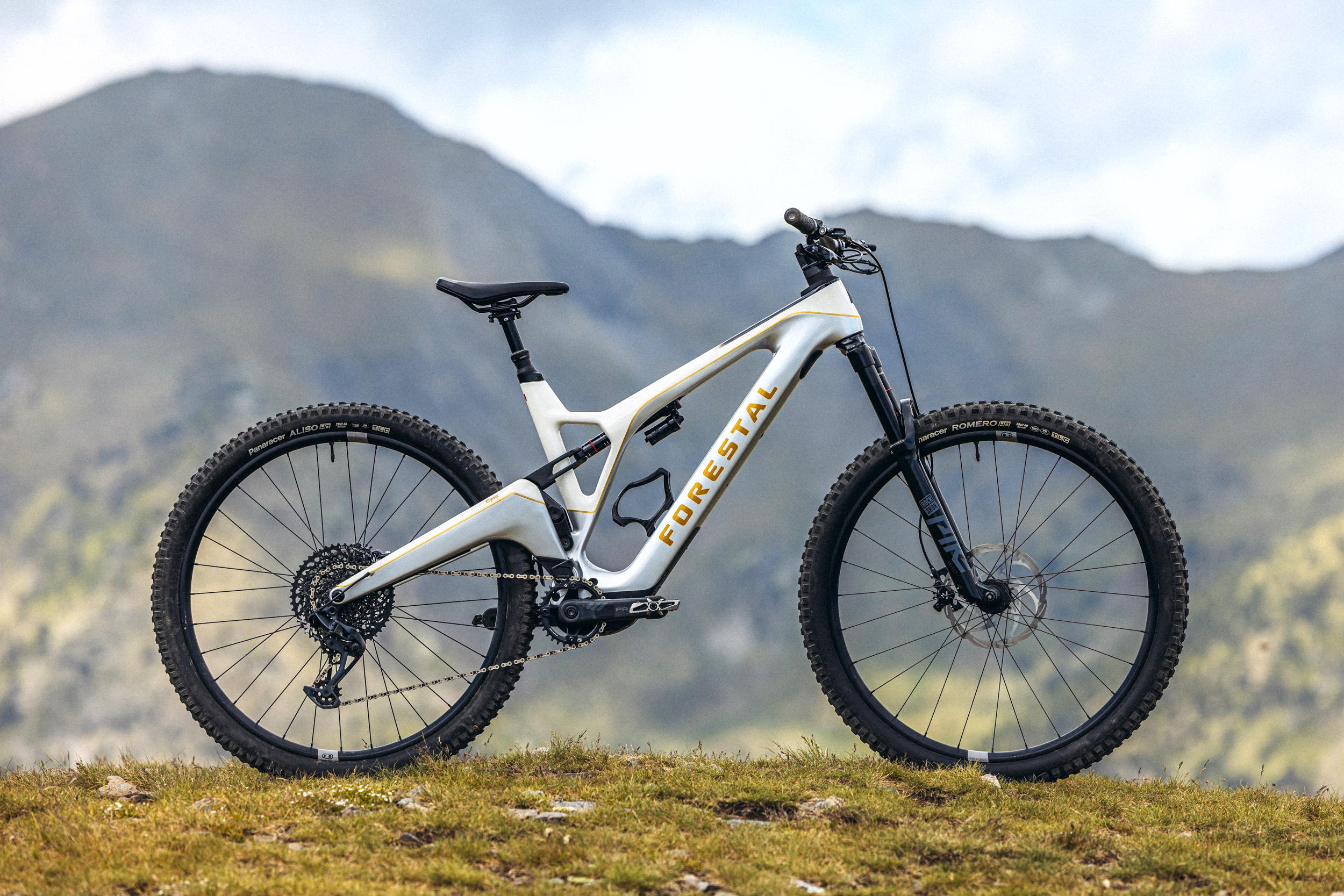
Forestal was looking to utilise this technology to bring its frame manufacturing in-house to Andorra.
European manufacturing
Focus has partnered with Rein4ced in Belgium to produce the Jam2 NEXT. This has further advantages for the German brand in terms of cutting supply chains – a key concern with rising tensions across the globe – reducing the cost and carbon emissions of shipping products from Asia, and allowing for more production flexibility.
Felix Stix, Senior Product Manager at Focus Bikes said:
“Carbon fiber is the ultimate material when it comes to performance bikes of all categories. The majority of the performance-oriented cyclists crave the technical and emotional benefits of carbon fiber bike frames. Those frames come at a big ecological cost that clashes with the growing eco-conscious mindset in those target groups.
Our JAM² NEXT research and development project set out to find a solution to the ecological question marks of traditional carbon bicycle frames. And therefore a product that meets the needs and desires of our target group in the future.”
Paul Sadowski, Senior Sustainable Design and Materials Engineer further commented:
“In 2017, we set out in search of an automated manufacturing process to be paired with a new type of carbon that could be recycled at the end of its life cycle. And we found it.
With this project, we aimed to build a proof of concept: designing an e-mountain bike frame around a new, recyclable carbon material, for a highly automated production process while keeping the product’s end of life in mind to minimize its ecological impact.”
We’ve reached out to Focus for further information on if and when this new frame technology will make production. Stay tuned for further updates.